How Thickness of Hot Stamping Foil Affects Its Function
Hot stamping foil is multi-layered. The thickness of film layer, adhesive layer, and top layer varies per different industrial needs. The following provides how the structure has impacts on hot stamping process.
What Are the Impacts of Thickness of Film to the Stamping Process?
If the film is creased during the process because it's too thin, the creased parts will no longer be usable. Thicker film has stronger structure which allows it remain stable during the process and hence causing a lower defective rate.
Summary:
The thickness of film is based on conditions of hot stamping.
Thick | Thin | |
---|---|---|
Processing Speed | Slow | Fast |
Stamping Temperature | High | Low |
Stamping Time | Long | Short |
Strength | Strong | Weak |

Thicker adhesive layer is required for working on frosted surface.
What Are the Impacts of Thickness of Adhesive Layer to the Stamping Process?
The thickness of adhesive layer doesn't directly affect yield rate, instead, the major concerns are cost and time of production. The thinner it is, less time and cost needed. However, thin adhesive layer it is not suitable for every product. Substrate with matte and frosted surface requires thicker adhesive layer to fully attached to the uneven surface and assure good adhesion.
Summary:
Thin can save time, thick can be applied to uneven surface.
Thick | Thin | |
---|---|---|
Cost | High | Low |
Stamping Time | Long | Short |
Suitable For | Various substrate | Limited to smooth surface |
Stamping Area | Large area | Small area |
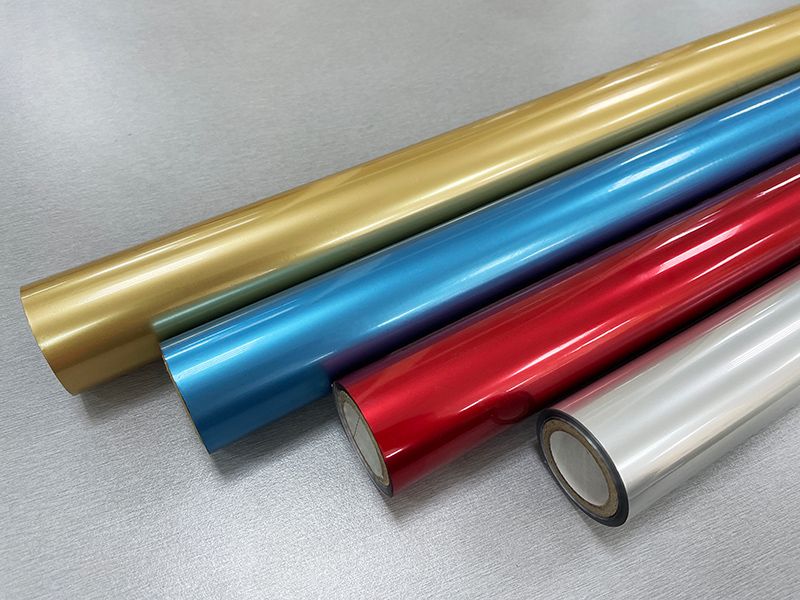
Higher temperature is necessary for using hot stamping foil made of matte.
What Are the Impacts of Thickness of Top Layer to the Stamping Process?
The thickness of top layer is usually fixed. Matte material will be added into top layer under special circumstances to make the foil thicker, like matte color foils, so the thermal conduction would be slower.
Summary:
It requires a. larger presser, b. high temperature, c. longer stamping time to assure the successful making of the end products.
- Related products
Plastic Packaging Hot Stamping Foil
Hot stamping foil for plastic packaging has high chemical resistance and good adhesion to various plastic materials so the trademark or logo of the products won't come off. Suitable for industries such as cosmetics product packaging materials, household appliances and so forth.
Hot Stamping Foil for Glass and Ceramics
Designed for Premium Products, Combining Luxury and Durability
Glass and ceramic hot stamping foil is a high-performance metallic transfer film specifically designed for glass hot stamping processes and ceramic applications. It is ideal for premium products such as perfume bottles, cosmetic bottles, wine bottles, and decorative vases. This product not only delivers exceptional high-gloss hot stamping effects but also offers the durability of scratch-resistant glass transfer and the stability of alcohol-resistant hot stamping, making it the perfect solution to meet the demands of the high-end market.Moreover, the product complies with multiple environmental and safety certifications, including REACH, RoHS, EN71-3, and CP65, ensuring market safety. Environmentally certified hot stamping foil not only enhances product value but also meets the stringent environmental requirements of the international market.Whether you aim to enhance the visual appeal of your products or strengthen their functionality, our hot stamping foils will help you stand out in the competitive market.
Lamination Film
Lamination film could be fully attached to various substrates such as plastic and paper, allowing them to exhibit gloss. The difference between hot stamping foil and lamination film is the PET film layer is kept after the laminating process, leaving an extra protection to the surface of the products, keep moisture and oxygen away. It could work as a protective film. It also has better abrasion resistance and scratch resistance than general hot stamping foil, and have great adhesion to various substrates such as labels, greeting cards, wine bottles, packaging paper boxes, lampshades, etc.
Holographic Foil
Holographic foil requires excellent hologram embossing technology to display a special appearance and catch customers' attention. The foil is often used in hot stamping on various papers and plastic materials and facilitate decorative functions. It could be applied to cosmetics, paper box, lure bait, credit card, passport, and anti-counterfeit label, it is flexible and available for satisfying different, customized layouts, colors, and patterns.